Industrial Robots Range
- industrialrobots
- Feb 26, 2021
- 5 min read
At the Ericsson Blog, we provide insight to make complex ideas on technology, innovation and business simple. In the Ericsson Technology Review article mentioned above, our colleagues elaborate on the topic of flexibility as a success factor for industries, and the role that 5G can play in that context. The market is projected to grow at a CAGR of 15.1% during the forecast period. As per Fortune Business Insights, the market was worth USD 21.83 billion in 2019.
A robot automation project can be challenging, especially for companies with no prior experience. High capital expenditure is required, not only for the purchase of the industrial robots, but also for integration, programming, and maintenance. In some cases, a custom integration may be required, which can further drive up the overall cost. Companies may not always have the necessary space and infrastructure for deployment of robots.
Key Market Trends
Investigated KPIs are response time and precision of trajectory execution, i.e. spatial and temporal deviations from the planed trajectory. The measurement results have shown that the network delay lower than 4 ms has no significant performance impact. This is because the internal operation of the robot ends in about 2 ms standard deviation in response time due to the internal sampling used in the robot, and the ticks of the robot and the controller are unsynchronized. This is pretty much the typical machine people think of when they think of industrial robots. Fanuc is the largest maker of these type of robots in the world and they are almost always yellow. This robot has six independent joints, also called six degrees of freedom.
The truth is, while industrial robotics certainly vary in their levels of complexity, even the simplest application of an industrial robot is a far cry from plug and play functionality. To put it another way, a robot arm that requires limited movement within the X, Y, and Z axis to perform its task day in and day out requires more than just a few lines of code.
Talk to us to see if, when, how, and where automation would make the most sense—and have the biggest impact—in your operation. + Pull entire layers off a pallet with a specialized pallet layer handling robot. Stäubli designed the 4-axis FAST picker TP80 robot for high-speed handling operations of small parts. The company is still one of the leading electrical and electronics companies in the world. Toshiba, a massively large Japanese conglomerate, used to be one of the world’s best-known companies before MP3 music players emerged. Capable of a variety of complex tasks, NextAge is helping Kawada find new partners in a variety of sectors. Already being put to use in a number of factories, the so-called “NextAge” robot is being presented as the next generation of robot worker.
Assembling, welding & soldering and pick and place application is expected to surge a considerable growth in the forecast period. Growth is likely to be driven by a rise in automotive, metal machinery, electrical and electronic industry where customized spare parts are assembled and installed in the finished product. Robotic devices are already establishing a wide presence in several commercial industries. As robotic technologies become more affordable, they will soon be available in various forms for consumers as well, with the ability to impact our lives in countless ways.
All components and solutions must interact seamlessly and error-free to ensure an industrial robot operates properly when deployed. A robot must always be protected against unauthorized modification of its configuration and calibration data. On a whole, the advanced capabilities of today’s industrial robots require very high quality and safety standards. This includes following a safety-certified development process for safety-critical system components.
The robot is customizable, meaning users can add sensors, robotic arms, or different payloads to complete a task. The parallelograms move a single end of arm tooling in a dome-shaped envelope. They are used primarily in the food, pharmaceutical, and electronic industries. The robot itself is capable of precise movement, making it ideal for pick-and-place operations. A SCARA robot is mainly used in assembly applications due to the nature of its movement, such as jobs that require drilling or tapping assemblies. In many automotive plants, robots are assembling smaller components like pumps and motors at high speeds. Often, robots are performing tasks like windshield installation and wheel mounting to increase throughput.
In his spare time, Siôn enjoys heavy metal concerts, family walks and John le Carré novels. Many of the jobs in this list will also become redefined as opposed to totally eradicated, with skills that can be transferable to other roles. Flexibility and a willingness to change careers will be an important attribute in the future job market. None of this looks good for professional fishers, who are subject to ever stricter quotas as a result of these developments. Even the few who choose to remain in the profession will be unlikely to escape technology, with research underway into fishing ‘bots’ that can do the job instead of humans. Many telemarketing companies have adopted this new approach that negates hiring costs and can engage potential customers at any time of the day or night.
Industrial applications require a proven and robust solution for wireless connectivity. Analog Devices offers the only wireless networks designed for the harshest industrial environments where low power, reliability, resilience, and scalability are key. In the future, 5G will be an enabler, directing robotic mobility around the factory floor and in remote locations. Advance motion and robotic designs with high precision position feedback solutions. High resolution space constrained optical encoders require small high precision signal processing and robust communications.
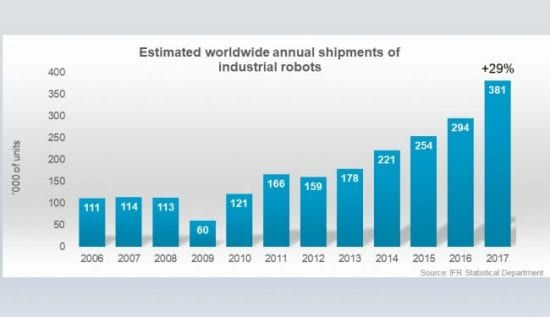
The control box consists of a powerful motion controller, motion drives, a robot controller and power supplies. Depending on the robot type, the manipulator is made of a set of movers or actuators, sensors and electrical brakes.
A parallel manipulator is designed so that each chain is usually short, simple and can thus be rigid against unwanted movement, compared to a serial manipulator. Errors in one chain's positioning are averaged in conjunction with the others, rather than being cumulative.
In the last years, they became general-purpose tools for automating production processes. Since their application possibilities are constantly being expanded they are used everywhere as long as the benefit of automating is higher than the efforts and costs of buying, installing and programming the robot. The robot's joint structure allows it to be compliant to forces in the horizontal plane. This is important for "peg in hole" type applications where the robot will actually flex to make up for inaccuracies and allow very tight part fits. If you look closely you will see two cylindrical pistons on the side of the robot.
However, hydraulic drives are more prone to maintenance issues and carry the risk of oil leakage, which can create a fire hazard in enclosed spaces. Hydraulic robot systems are also less suited for indoor work in controlled environments where they are in close proximity to personnel. Pneumatic actuators are commonly used for powering the mechanisms that interact with external objects, such as the grippers mounted on the end of electric-drive robot arms. A pair of pneumatic actuators working in unison to power a single gripper can enable it to move along multiple axes.
Comments